
Since 2019 when the first generation of “hero samples” recycle ready mono-material stand-up pouches were presented, BOBST and Brückner Maschinenbau, along with the other project partners comprising leading polymers and consumables suppliers, have made significant achievements in the mission to develop state-of-the-art solutions that help the meet the industry’s pledges about packaging sustainability.
Within the ecosystem of partners involved, the contributions of Brückner Maschinenbau and BOBST in the development of a series of new generation high barrier mono-material laminated BOPE- based structure for sustainable flexible packaging solutions have been in the field of film technology and in their functional properties and end-to-end processability respectively.
Brückner Maschinenbau is a market leader for biaxial (BO) film stretching lines. With its competence, the good performance of biaxial stretched polypropylene and polyethylene films regarding barrier value and processibility could be achieved.
BOBST’s Competence Centers have been used to test the viability of the new substrates, which differ from conventional ones in terms of machinability. Because BOBST can offer all technologies for production of flexible packaging, from vacuum metallizing and coating, through to gravure, CI and inline flexo printing, to lamination, it had been possible to check and validate the given requirements at every stage of the production process.
“Finding sustainable alternative to non-recyclable flexible packaging is a very challenging endeavor as there are so many different aspects that need to be considered and dealt with so that all requirements are met and solutions are fully sustainable across all areas of their life cycle” explains Nick Copeland, R&D Director Barrier Solutions at BOBST “Between finding the flexible packaging best materials and end-of-life options that have the least environmental impact, there are many industry requirements to be met in terms of substrate processability, barrier levels, safety and optical quality of the packaging to name but a few.”
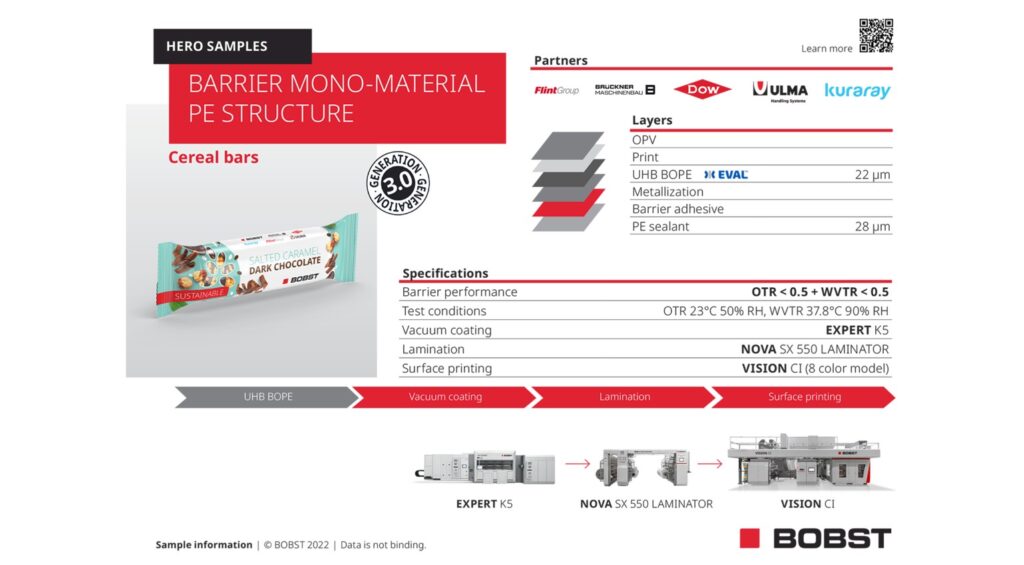
“Brückner is convinced that the future will continue to belong to plastics if they are used and reused sustainably,” said Helmut Huber, COO Sales & Project Management, Brückner Maschinenbau GmbH & Co. KG. “As part of a circular economy, the undeniable advantages of plastic can be combined absolutely well with the sustainability goals of a modern society. Regarding the discussions about recycling targets for plastic packaging, we see mono-material packaging structures clearly on the rise.”
Since the first generation of Hero Samples, the partners involved have continued their considerable investment and R&D research to progress the sample further. Latest hero samples 3.0 include full PE and PP monomaterial structures with option of AlOx transparent metallizing or AluBond opaque metallizing, or conventional metallizing, using barrier adhesives, to achieve flexible packaging structures offering high and ultra-high barrier protection levels.